A Luthier's Life
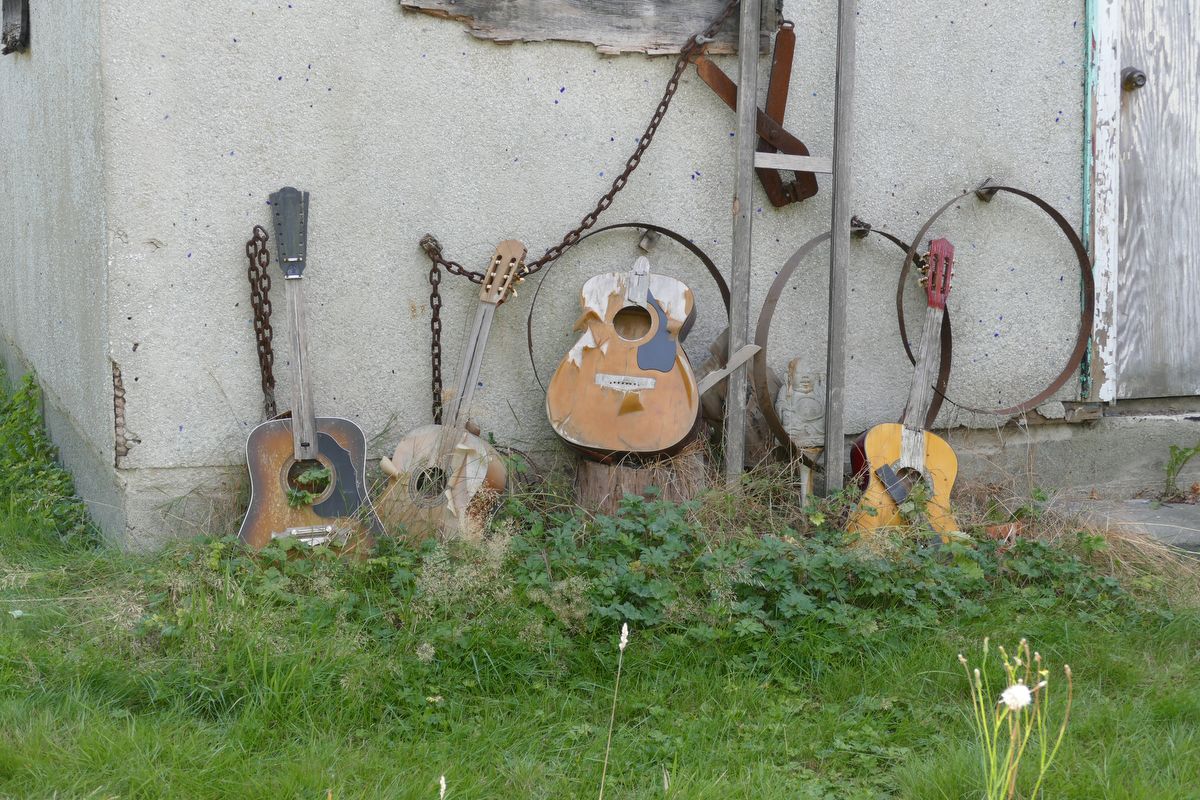
'I got very lucky'
Ed Bond never imagined that he would build guitars for a living. As a kid he dreamed of being a professional musician one day. But after all these years, he says, it was his skill for wood-working combined with a relentless passion for guitars that led him down a different path.
He got his first taste for making guitars when he began working at Larrivée Canada's Vancouver factory back in 1996. Starting with the very basics of constructing guitars he frequently moved around the shop floor, learning each step of the process. He even spent his last 12 years at Larrivée overseeing the assembly line as a production and quality control manager.
But when Bond sensed that Larrivée was slowing down its operations in Canada, he began building guitars off-the-clock and experimenting with his own designs from home. Just a few years later, the company shut down its Vancouver plant and moved shop to Oxnard, California where they remain today. In spite of being a casualty of Larrivée's defection to California, Bond saw his unemployment as a golden opportunity. In 2012 he launched Halcyon Guitars, realizing a new dream of building guitars from scratch right at home in East Vancouver.
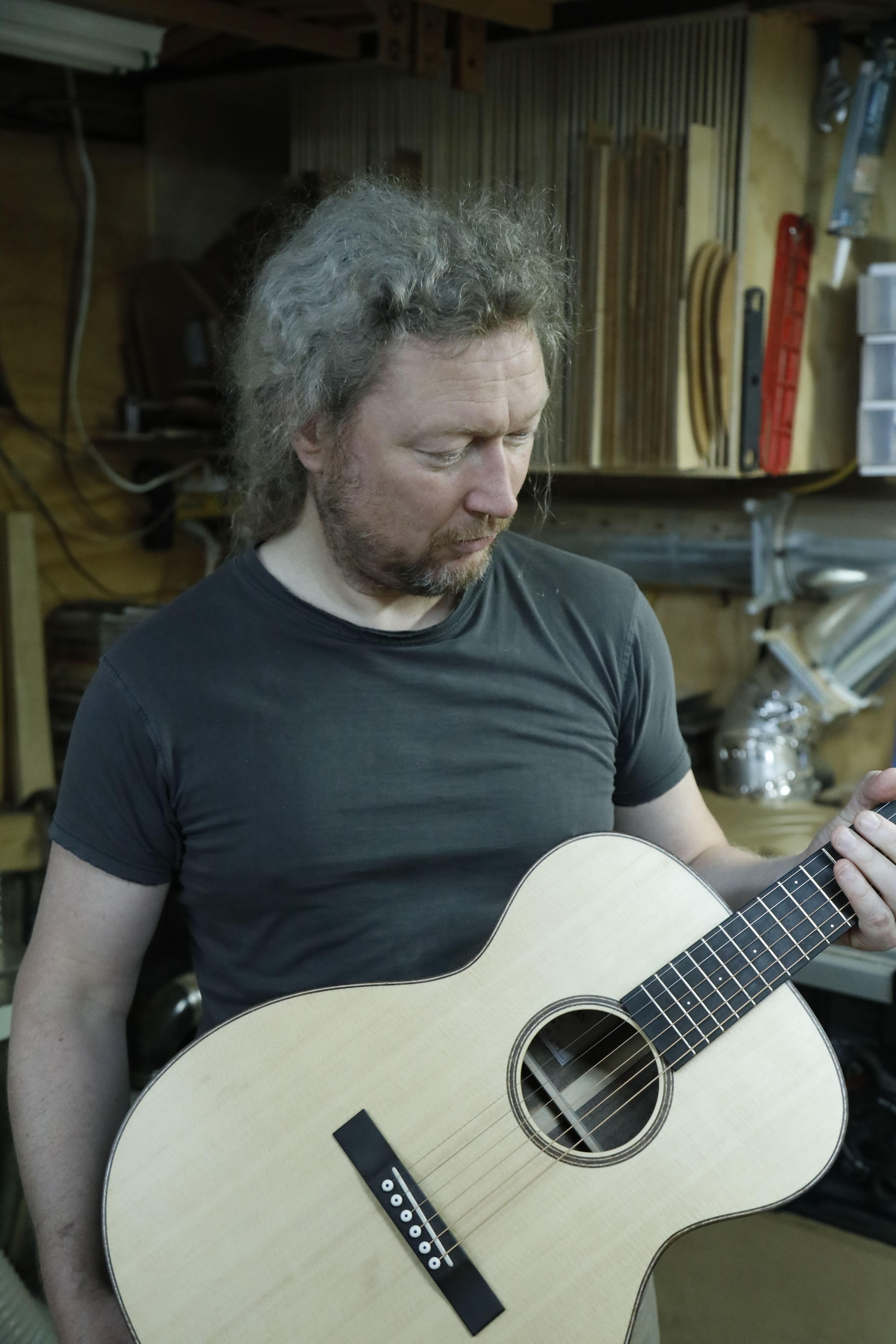
Bond holding a finished guitar built for musician Stuart Chatwood from the 'Tea Party'. (Photo: Austin Westphal)
Bond holding a finished guitar built for musician Stuart Chatwood from the 'Tea Party'. (Photo: Austin Westphal)
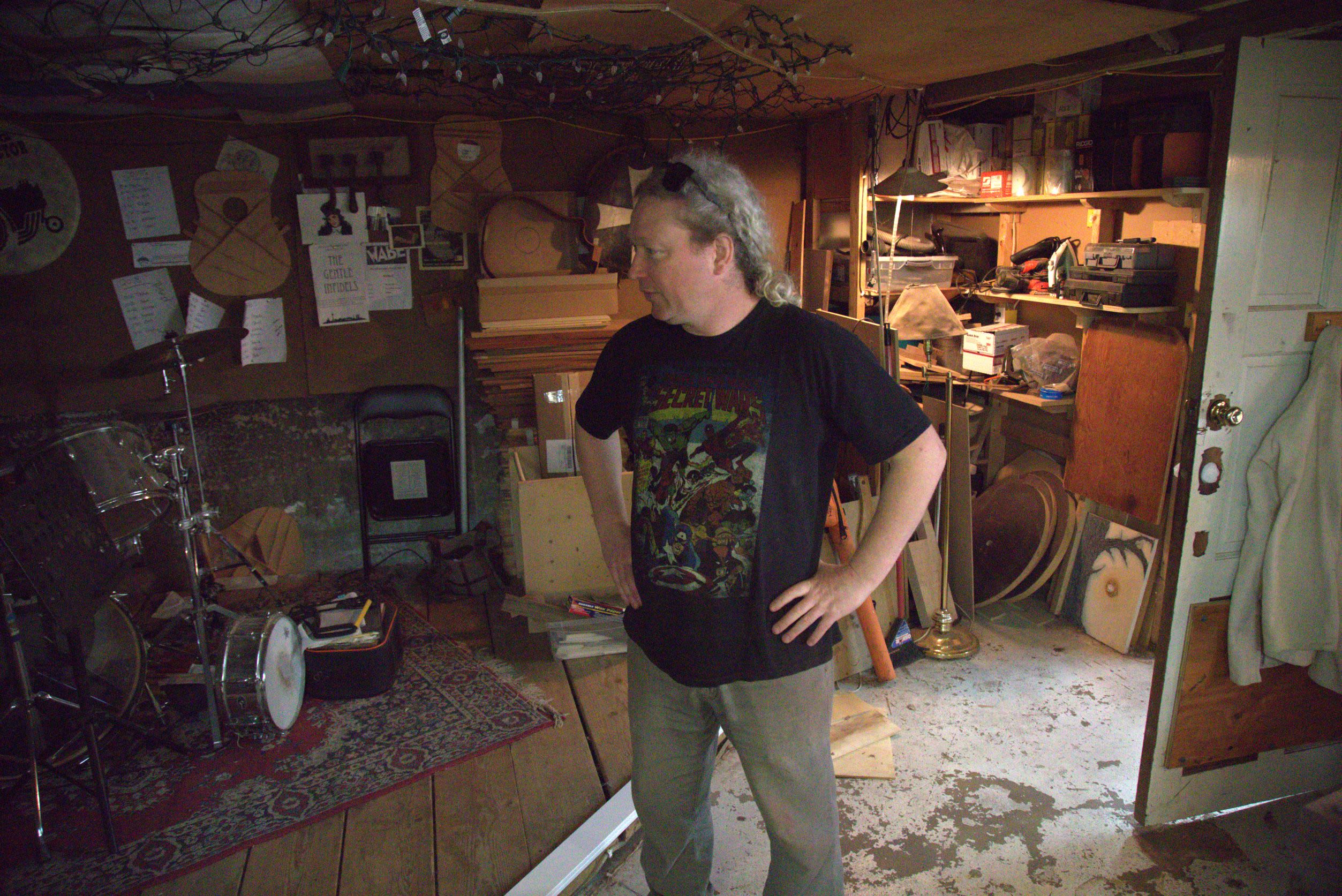
Inside the Halcyon Guitar workshop with luthier Ed Bond. (Photo: Austin Westphal)
Inside the Halcyon Guitar workshop with luthier Ed Bond. (Photo: Austin Westphal)
'I'm just winging it in here'
When standing outside the entrance to the basement of Ed Bond's East Vancouver home, it's nearly impossible to tell what goes on inside — other than the suggestive facade of a small graveyard of vintage guitars. It's not the place you might imagine when you think of a craft person's workshop. Descending into the basement you find yourself in a dark, chaotic and cluttered labyrinth of claustrophobic rooms that have been converted into a intimate space where guitars are crafted by hand. Permeating the air is a warm and earthy scent of wood, immediately transporting you into a forest of maple, mahogany, red cedar, spruce, rosewood, walnut and cherry. Despite its appearance, it's a mesmerizing place. And for Bond, everything has a purpose. It's a venue of necessity where Bond, with the supple hands of a master crafts person and an eye for balance and precision, transforms materials harvested from nature into musical instruments of beauty.
Unlike other B.C. luthiers building custom guitars to order, Bond focuses his efforts on employing simple designs with minimal decorative elements to keep the price of his guitars more affordable to his customers. But when you hold, scrutinize and play one of his finished instruments, you discover there is nothing budget about them. They are worthy and robust instruments meant to be played. The quality is pronounced. Whether cradled in the arms of an enthusiastic novice or commissioned into service by a performing artist, everything that makes a musician smile is there.
Sound comes first and foremost for Bond. He conducts deflection and resonance testing on the body of each guitar, which is what he says separates his guitars from those of mass manufacturers like Martin, Taylor and Gibson. Exactly how he does it remains an industry secret. "When you compare the finished guitar to other things in its price range, the difference between a handmade and mass-produced guitar is pretty clear," Bond says. "There's a pretty dramatic, noticeable and audible difference in the tone and playability of a handmade guitar. It's distinct."
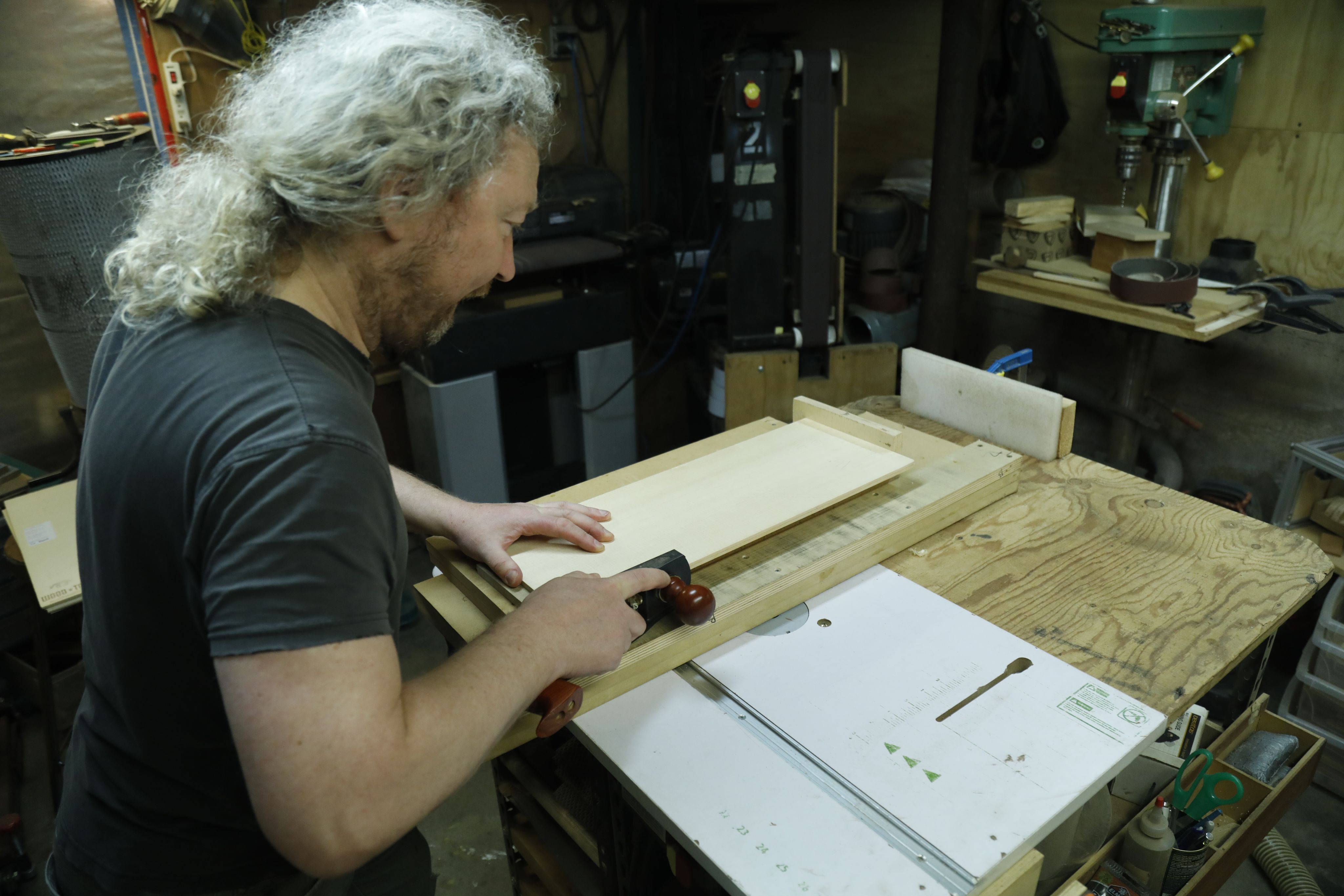
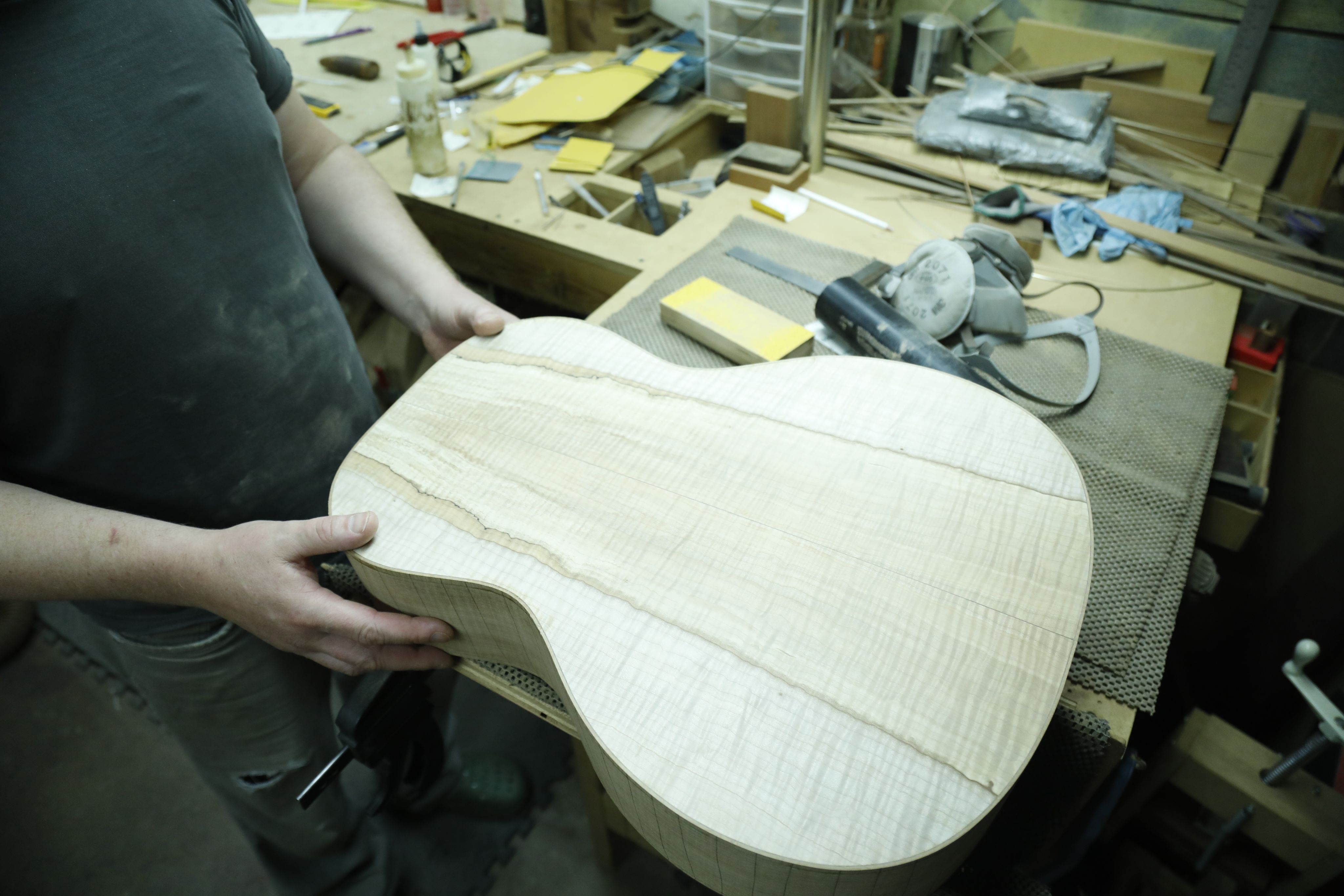
'I'm still working on it'
Growing his business, Halcyon Guitars, hasn't come without its challenges and setbacks, however. From low margins and long hours to competition with large commercial manufactures and a high risk of financial failure, surviving as a luthier can seem daunting. Needless to say, Bond must overcome barriers everyday to keep his operation afloat. Since the loss of his apprentice several years ago he's become a one-man production line. He handles sourcing of materials, construction, banking, website maintenance and everything in between by himself.
Each guitar he makes requires an investment of around 100 hours of labour on average, sometimes more depending on the order. Making about 40 guitars every year, it adds up to 4,000 hours of work for Bond — over twice the 1,644 hours worked on average by Canadians in 2020, according to Statistics Canada. And working in confined quarters only adds to the time it takes to build a single instrument — constantly needing to clear space and move equipment with each stage of production. He continues to sell his guitars at a base price of CAD $1,899 as it's his best way of competing with other local luthiers and large manufacturers. It may be a great bargain for the consumer, but it certainly comes at a cost.
Still, he would rather work grueling hours to make more guitars than raise his prices. And despite the challenges of working out of his rented basement, it's actually the low overhead cost while selling directly to consumers that helps keep his dream alive. His dedication to building quality instruments at an affordable price is the reason for his success, enjoying a cult-like following on Facebook, Instagram and online guitar forums. He's come a long way since his days at Larrivée and is gradually making a name for himself in the guitar world. He hopes to rise from the basement one day and become a true industry contender. To achieve this he'll need things like a commercial workshop space, new apprentices and most importantly, bank financing.
But through all the trials and tribulations, Bond manages to maintain his enthusiasm, passion and sense of humour — which he says is necessary for survival in an unforgiving industry.
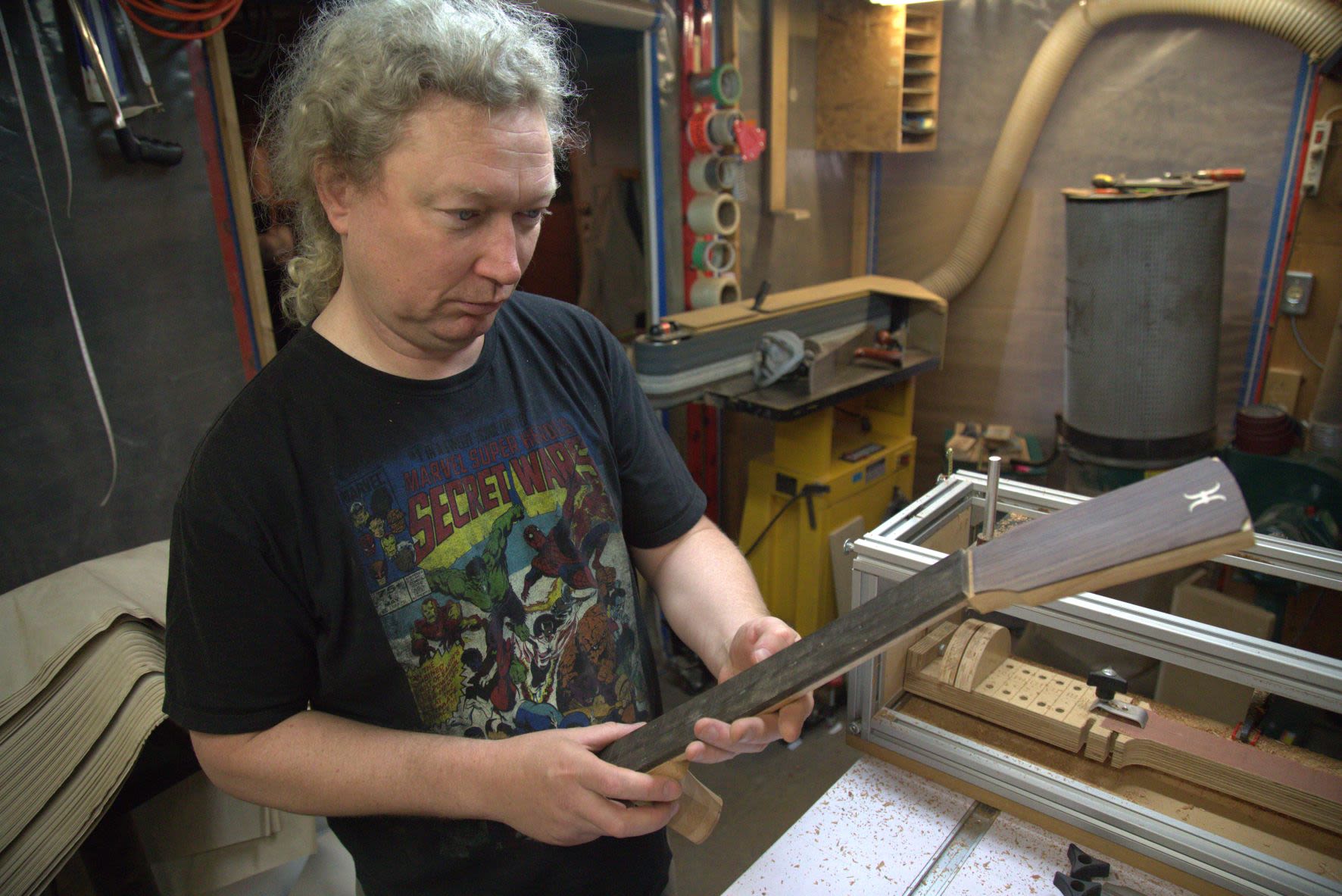
Bond inspects a recently completed neck and fingerboard. (Photo: Austin Westphal)
Bond inspects a recently completed neck and fingerboard. (Photo: Austin Westphal)
'I don't know if it's truly sustainable'
The emerging challenge luthiers everywhere face is procuring quality wood suitable for building guitars. Global deforestation has decimated the supply of tropical species native to Africa, Asia and South America, which are all highly desired in guitars and other musical instruments. International restrictions on the sale and importation of endangered species like Brazilian and Indian rosewood, Madagascar ebony, Spanish cedar and mahogany create a rapidly dwindling and finite supply. This means that small and large scale manufacturers alike have to resort to sourcing wood from questionable sources in addition to paying a hefty premium.
And Bond is no exception. That's why he's taking a different approach with his Halcyon Guitar brand. Like most luthiers, he still uses some exotic woods, although sparsely. But he's committed to sourcing more wood straight from his backyard in British Columbia, not only to cut the cost of shipping and tariffs, but to ensure a more sustainable future for boutique guitar makers like himself. "We live next door to the most important parts of the guitar," he says. "All of the wood I use for most guitars comes from northern B.C. and the pacific northwest."
Using lower grade cuts of wood keeps the cost down and is more environmentally responsible, he believes. And there's no compromise in the sound. "Most luthiers will acknowledge that a lower grade cut of wood can be made to sound excellent, as long as you build properly with it," Bond says. "Higher grade cuts of wood do not always guarantee a good sounding guitar." But Bond still has grave concerns about sustainable forestry in Canada, especially when it comes to the future B.C.'s old-growth forests, which are renown for their tonewoods. "They've been saying that in ten years we're going to run out of spruce and at some point it will probably be true," he says. "And I have definitely noticed a sharp decline of quality woods available." Bond is aware of the impacts of over-logging on climate but his greatest fear is that it will disproportionately affect small businesses like Halcyon Guitars. "It's going to be a problem. Whoever has the money to buy in advance will win."
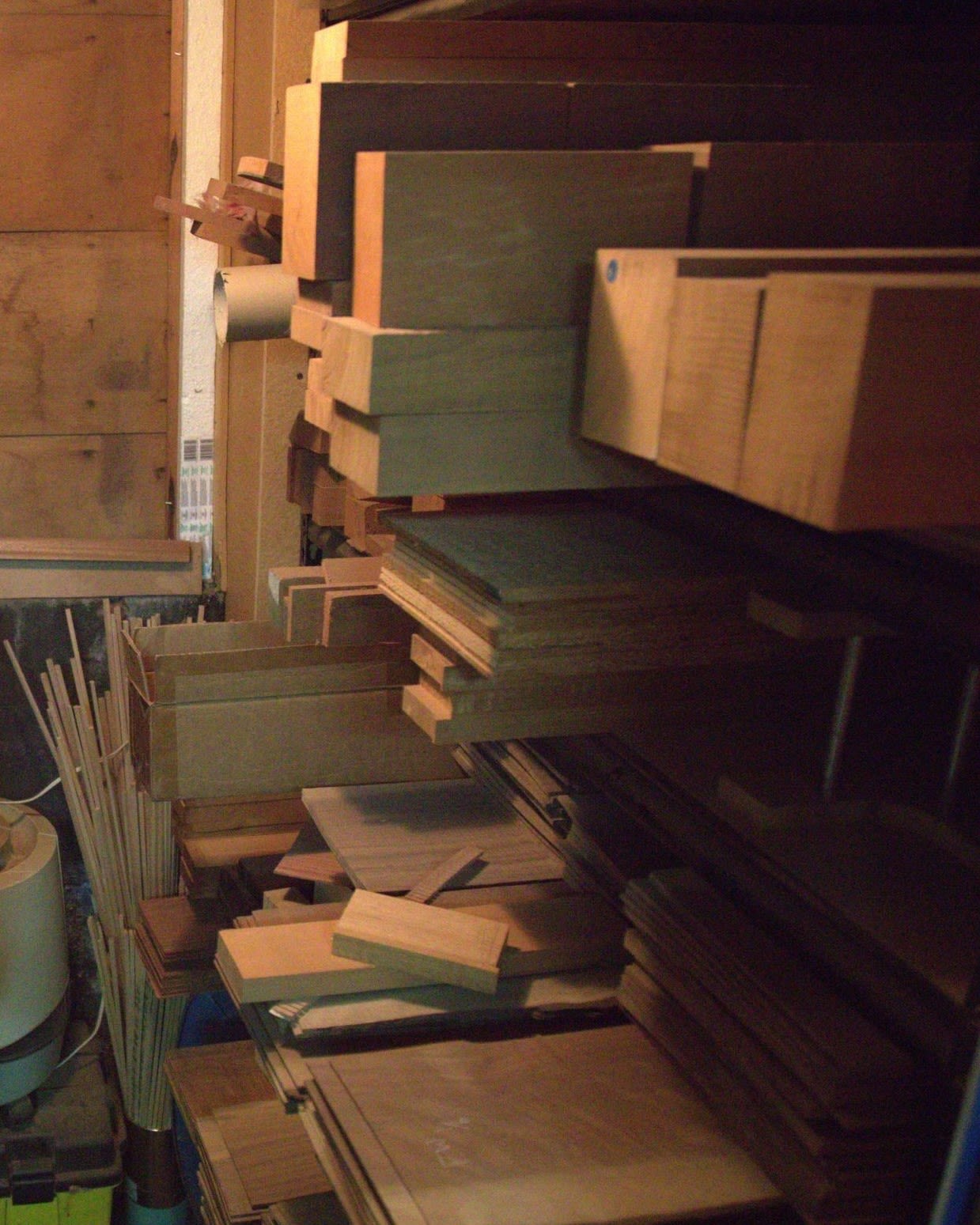
Bond's woodshed (Photo: Austin Westphal)
Bond's woodshed (Photo: Austin Westphal)
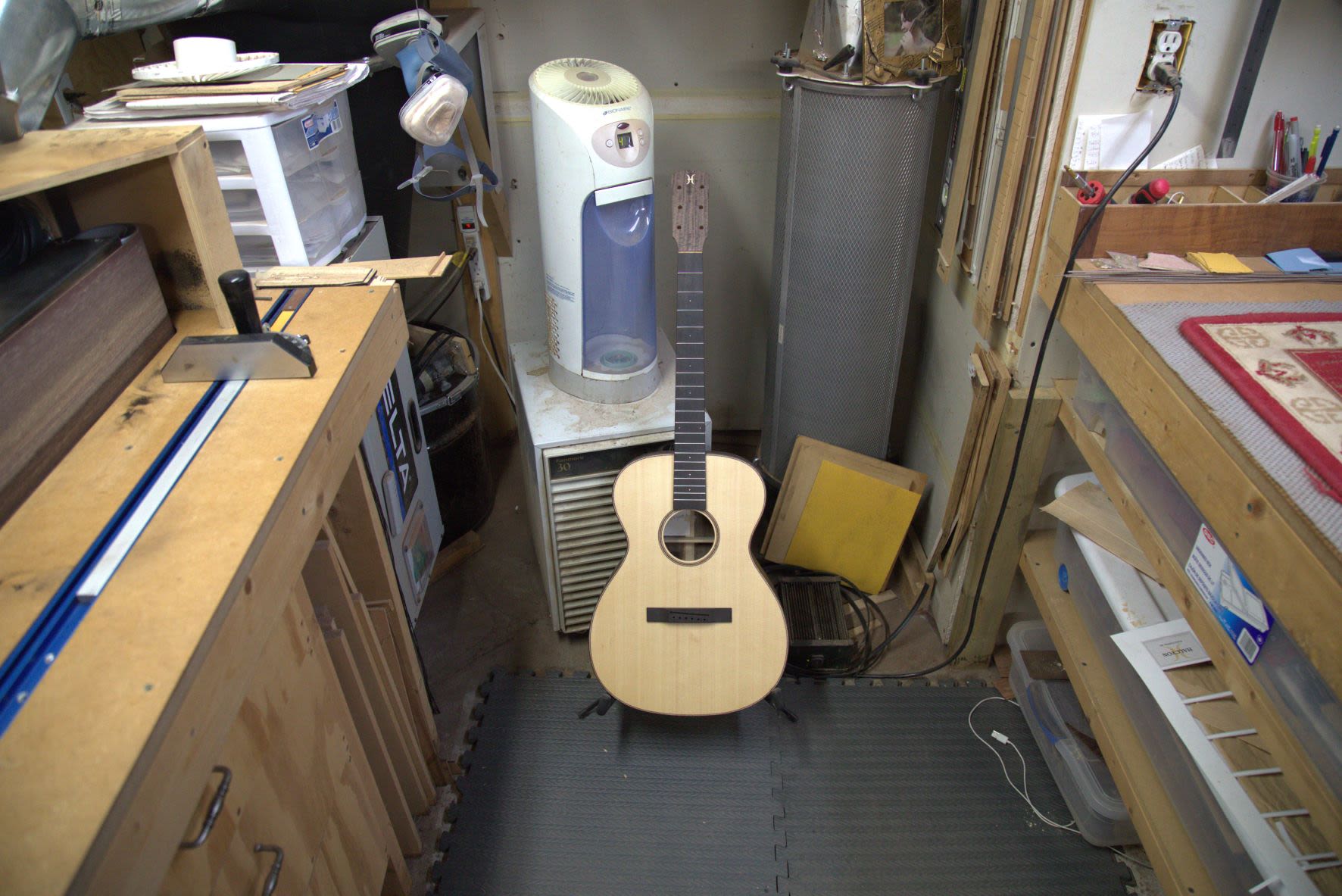
A near-finished guitar ready for a set of strings and resonance testing. (Photo: Austin Westphal)
A near-finished guitar ready for a set of strings and resonance testing. (Photo: Austin Westphal)